10 Powerful OKR Examples in Production Operations
Production operations are vital for organizations to ensure efficient and effective manufacturing processes. Objectives and Key Results (OKRs) can play a significant role in driving performance and success in production operations. Here, we present ten powerful OKR examples in production operations that offer valuable insights for organizations aiming to excel in this area:
1. Increasing Production Efficiency
Objective: Improve production efficiency and optimize resource utilization.
Key Results:
- Reduce production cycle time by 20% within the next quarter.
- Achieve a target production output of 10 units per day.
- Minimize machine downtime by 15% through proactive maintenance and optimization.
2. Enhancing Product Quality
Objective: Improve product quality and minimize defects.
Key Results:
- Decrease the number of product defects by 20% within the next six months.
- Achieve a customer return rate of less than 30% due to product quality issues.
- Increase customer satisfaction ratings related to product quality by 15% within the next year.
3. Streamlining Supply Chain
Objective: Optimize supply chain processes to improve overall production flow.
Key Results:
- Reduce lead time in the supply chain by 15% for critical components/materials.
- Achieve a target inventory turnover ratio of 1:2 within the next fiscal year.
- Improve supplier delivery reliability to achieve an on-time delivery rate of 20%.
4. Implementing Lean Manufacturing
Objective: Adopt lean manufacturing principles to eliminate waste and improve productivity.
Key Results:
- Implement 5 continuous improvement projects to reduce waste and improve efficiency.
- Achieve a 12% reduction in non-value-added activities within the production process.
- Train 70% of production staff on lean manufacturing principles and tools within the next six months.
5. Enhancing Workplace Safety
Objective: Ensure a safe working environment and reduce workplace accidents.
Key Results:
- Achieve 0 lost-time injuries within the next fiscal year.
- Conduct safety training for all production employees and achieve a 90% participation rate.
- Implement 10 safety improvement initiatives based on employee suggestions.
6. Implementing Automation and Technology
Objective: Harness automation and technology to enhance production operations.
Key Results:
- Implement 6 automation solutions to improve productivity and reduce manual labor.
- Adopt 5 new technology tools or software to streamline production processes.
- Improve machine utilization rates by 12% through effective utilization of technology.
7. Increasing Production Capacity
Objective: Expand production capacity to meet growing demand.
Key Results:
- Increase production output by 15% to meet projected demand growth.
- Invest in new equipment or production lines to increase capacity by 12 units.
- Reduce setup/changeover time between production runs by 5% to maximize overall production capacity.
8. Enhancing Supplier Collaboration
Objective: Foster closer collaboration with key suppliers for improved production outcomes.
Key Results:
- Establish strategic partnerships with 5 key suppliers within the next year.
- Conduct regular supplier performance evaluations and achieve a 12% improvement in supplier ratings.
- Implement a vendor-managed inventory system with 5% of critical suppliers to improve supply chain visibility.
9. Improving Production Planning and Scheduling
Objective: Optimize production planning and scheduling processes for improved efficiency.
Key Results:
- Implement an advanced production planning and scheduling system within the next quarter.
- Achieve a 10% reduction in production lead time through better scheduling and sequencing.
- Improve on-time delivery performance to 75% of customer orders within the next six months.
10. Empowering Continuous Improvement
Objective: Foster a culture of continuous improvement within the production team.
Key Results:
- Encourage and implement 5 employee-driven improvement initiatives.
- Conduct regular Kaizen events or improvement workshops to generate 5 process improvements.
- Achieve a 10% increase in employee engagement scores related to continuous improvement efforts.
By adopting these OKR examples in production operations, organizations can enhance production efficiency, improve product quality, streamline supply chain processes, promote workplace safety, leverage automation and technology, increase production capacity, enhance supplier collaboration, optimize planning and scheduling, and empower continuous improvement. These strategic objectives and key results serve as guiding principles for organizations seeking to excel in their production operations and drive long-term success.
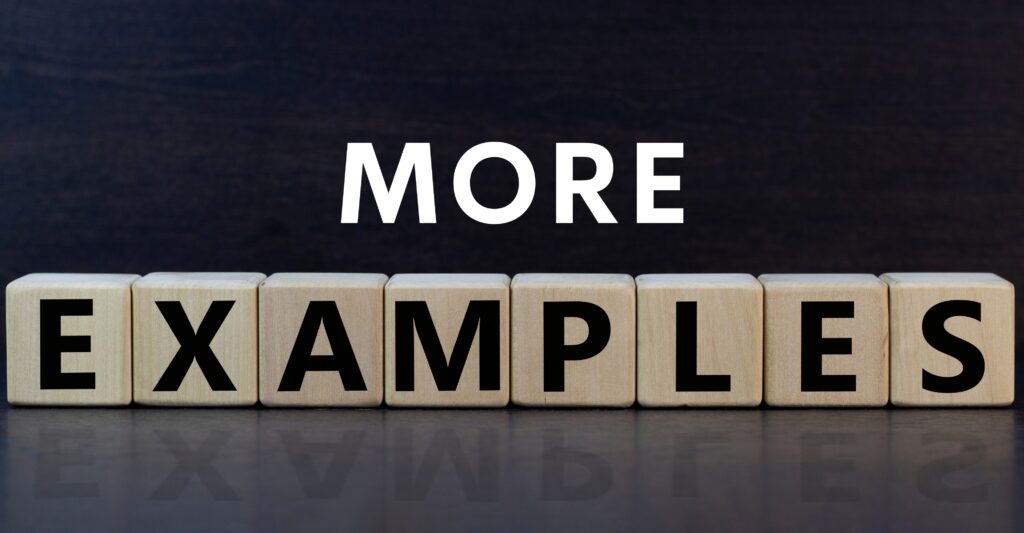
When looking to set OKRs, it’s natural to want examples to ignite the thought process or simply compare yours to OKR Examples. Check out our compendium of OKR Examples here.
Explore Our Range of Services
Bring OKRs (Objectives and Key Results) to your organisation with our tried & tested OKR Framework.

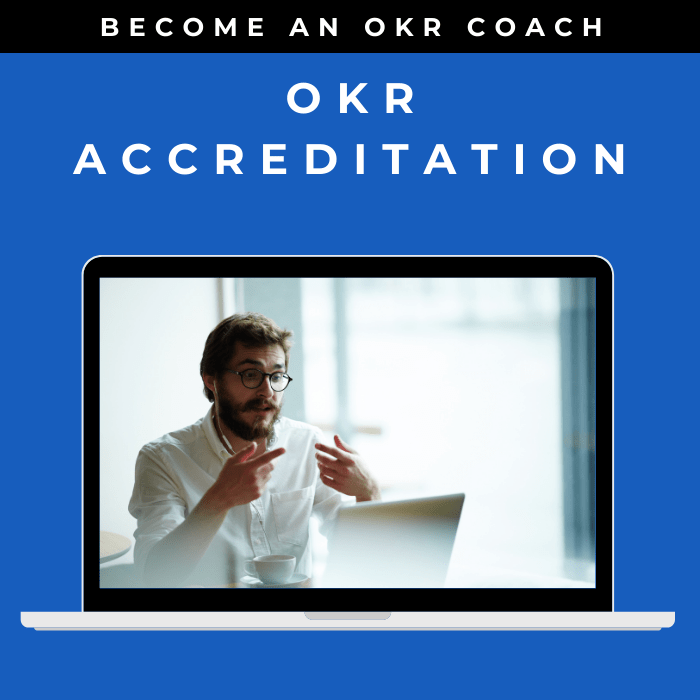
OKR International’s highly acclaimed Certified OKR Practitioner Program is the first and only OKR accreditation endorsed by ICF & HRCI for continuing education units.
OKR International helps leaders create the alignment, engagement and result orientation needed for growth by offering OKR Advisory services.
