10 Critical OKR Examples in Quality Control
Quality control is a critical function that ensures products and services meet the highest standards of excellence. Objectives and Key Results (OKRs) can be powerful tools to drive performance and improve quality control processes. Here are ten critical OKR examples in quality control:
1. Enhancing Product Quality
Objective: Improve product quality to meet or exceed customer expectations.
Key Results:
- Reduce the number of product defects or non-conformities by 50%.
- Achieve a customer satisfaction rating of 9 based on quality-related surveys or feedback.
- Increase the first-pass yield rate in production by 60%.
2. Strengthening Process Standardization
Objective: Establish and maintain standardized processes for consistent quality.
Key Results:
- Develop and implement 3 standard operating procedures (SOPs) for critical quality control processes.
- Achieve 70% compliance with established process standards across all production lines or departments.
- Conduct regular process audits and achieve a 70% compliance rate.
3. Improving Supplier Quality
Objective: Enhance the quality of materials and components supplied by vendors.
Key Results:
Establish 5 quality performance metrics for suppliers and rate them based on defined criteria.
Increase the percentage of approved suppliers based on quality assessments by 20%.
Reduce the number of supplier-related quality incidents or rejections by 50%.
4. Implementing Effective Quality Control Tools
Objective: Utilize quality control tools and methodologies to drive improvements.
Key Results:
- Implement 4 statistical process control (SPC) techniques in key production processes.
- Conduct root cause analysis and implement corrective actions for 60% of quality issues.
- Train 70% of quality control personnel on advanced quality tools and techniques.
5. Enhancing Process Capability
Objective: Increase the capability of critical processes to consistently meet specifications.
Key Results:
- Improve process capability indices (Cpk) to a target level of 8 or higher.
- Reduce process variation by 15% through process optimization or redesign.
- Achieve 20% reduction in the number of out-of-specification occurrences.
6. Strengthening Quality Assurance
Objective: Ensure compliance with quality standards and regulations.
Key Results:
- Conduct internal quality audits and achieve a 15% compliance rate.
- Implement 1 comprehensive quality management system and achieve certification.
- Achieve 40% reduction in the number of quality-related non-compliances or deviations.
7. Enhancing Customer Feedback and Satisfaction
Objective: Capture customer feedback to drive quality improvements.
Key Results:
- Implement a customer feedback system and achieve a 75% response rate.
- Use customer feedback to drive 40% improvement in product or service quality.
- Achieve a customer satisfaction rating of 9 based on quality-related surveys or feedback.
8. Promoting Continuous Improvement
Objective: Foster a culture of continuous improvement and innovation in quality control.
Key Results:
- Implement 1 structured continuous improvement program (e.g., Lean Six Sigma) for quality control.
- Achieve 80% participation of quality control personnel in improvement initiatives or projects.
- Generate 5 cost savings or quality improvement ideas through employee suggestions.
9. Enhancing Training and Skill Development
Objective: Develop the skills and competencies of quality control personnel.
Key Results:
- Provide training on quality control methodologies, tools, and best practices to 85% of the team.
- Achieve a 80% employee satisfaction rate with quality-related training and development initiatives.
- Conduct 3 regular performance reviews and identify individual development plans for quality control personnel.
10. Ensuring Regulatory Compliance
Objective: Maintain compliance with applicable quality standards and regulations.
Key Results:
- Conduct regular quality compliance audits and achieve a 70% compliance rate.
- Implement necessary changes to achieve full compliance with new quality regulations or standards within the next 3 months.
- Achieve a 40% reduction in the number of quality-related non-compliances or deviations.
By adopting these OKR examples in quality control, organizations can improve product quality, standardize processes, enhance supplier quality, utilize effective quality tools, and ensure compliance with regulations. These strategic objectives and key results serve as guiding principles for organizations seeking to excel in their quality control function and drive long-term success.
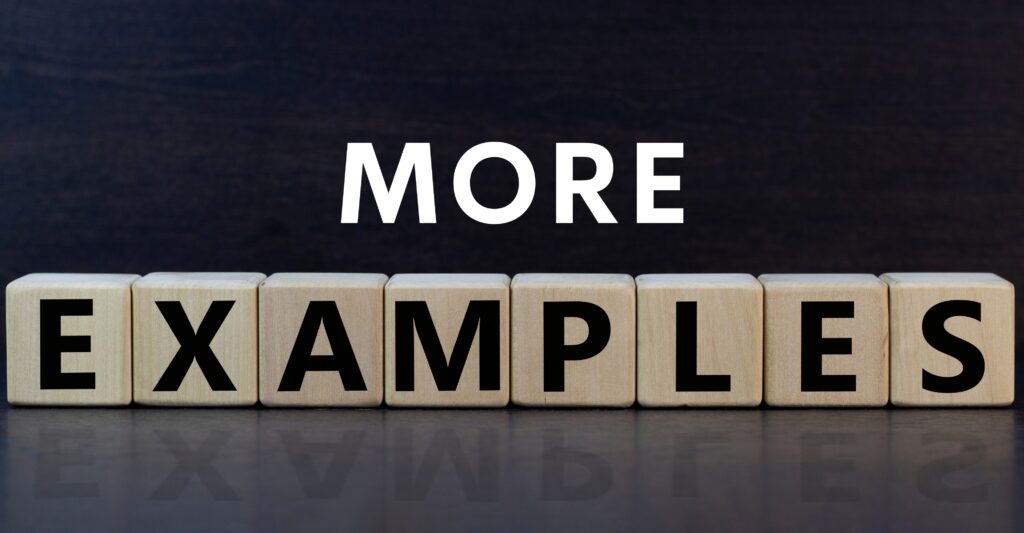
When looking to set OKRs, it’s natural to want examples to ignite the thought process or simply compare yours to OKR Examples. Check out our compendium of OKR Examples here.
Explore Our Range of Services
Bring OKRs (Objectives and Key Results) to your organisation with our tried & tested OKR Framework.

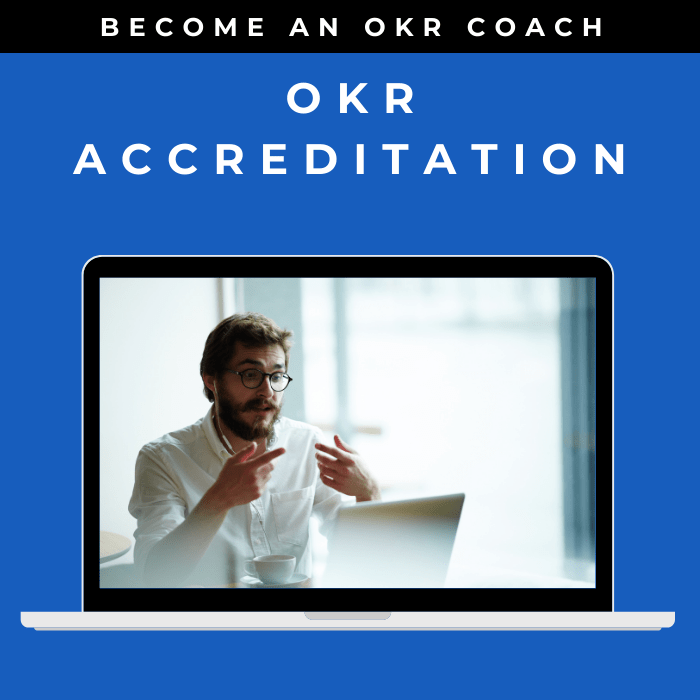
OKR International’s highly acclaimed Certified OKR Practitioner Program is the first and only OKR accreditation endorsed by ICF & HRCI for continuing education units.
OKR International helps leaders create the alignment, engagement and result orientation needed for growth by offering OKR Advisory services.
